巨豪自动喷涂设备资讯:塑料件保险杠涂装工艺及其设备特点
来源:巨豪机械 发布时间:2017/04/25 浏览:
近年来我国汽车保险杠行业的发展前景广阔,随着汽车车型的增加及产销量的扩大;保险杠和保险杠配件、的市场需求量也越来越多,这个汽车保险杠的生产企业带来了巨大的发展机遇,保险杠需求数量增长的同时,经济附加值增高,塑料保险杆的喷涂质量要求极为严格,从前处理、喷涂到固化的整个过程需要严格的控制,塑料件保险杠基材的特殊性决定了其与车身涂装工艺及涂装生产设备有很多不同之处。本文针对塑料件基材区别于车身金属材料的特点,重点介绍了其涂装工艺过程,并从工艺设计、涂料选择及设备配备等几方面分析了与车身涂装的区别。
保险杠在轿车上位置醒目,因而在外观质量等方面与车身同样重要,需要达到和车身同样的涂层外观性能和力学性能、化学性能。因此,塑料件保险杠的涂装工艺也有着非常严格的要求,可以作为汽车塑料装饰件涂装工艺的代表。
一、塑料件保险杠的特点
1.塑料件基材的特点
从涂装的角度看,保险杠常用的塑料基材改性PP(改性聚丙烯)具备以下特点:不易导电;表面能低,涂层难以附着;热变形温度低,为115~155℃;强度低。
2.保险杠的形状特点
保险杠的喷涂面积较车身面积小很多,且开孔较多。
二、塑料件保险杠涂装工艺及设备特点
针对塑料件保险杠本身所具有的特点,涂装作业需采取相应的处理措施,也就形成了塑料件保险杠涂装所特有的工艺。图1所示为塑料件保险杠的涂层组成,图2所示为其涂装工艺流程。
1.不易导电
(1)去静电、除尘塑料件不易导电的特性导致塑料件表面静电积存。静电的存在使得产品易吸附灰尘,影响涂装质量,因此喷涂前应除去静电及灰尘。塑料件保险杠涂装线上一般采用离子风对吹产品表面,既能除尘又能除静电(见图3)。多数生产线采用离子风刀装置,可以有效增大压缩空气的风力,形成强力而狭窄的均匀气流。气流带动离子发生器产生的高浓度正负离子吹向产品表面,移除灰尘的同时也清除了塑料件表面上的静电荷。
(2)导电底漆导电底漆的作用除了和普通底漆一样,可以对底材形成一层保护膜,从而得到良好的色漆涂装基础外,还有一个作用就是使涂层带电。如果色漆和清漆要进行静电喷涂,可以采用涂导电底漆的方法来使得底层导电,从而对上部涂层进行静电喷涂。
2.表面张力低
低表面张力的涂料易在高于其表面张力的表面上成膜,反之则很难成膜,因此,塑料件保险杠的表面张力低,从而导致涂料成膜困难,且涂层难以均匀地附着在产品上。
火焰处理(见图4)在高温下使塑料表面的大分子发生脱氢和氧化反应在保险杠表面生成氨基、羟基和羰基等含氧极性基团及不饱和双键,增加表面极性,从而增加表面张力,使涂料易于成膜。
塑料件保险杠涂装工艺及其设备特点
火焰处理工艺采用天然气混合空气燃烧,处理温度一般高达1000~2500℃,停留时间一般为2s左右。需要注意的是,由于塑料基材的分子在向表面迁移,处理过后的产品如果不及时进行涂装,一段时间(约2h)后基材内部的分子迁移到表面,表面能恢复到火焰处理前的状态,火焰处理的效果也就消失了。因此,火焰处理后应及时进行涂装。使用达因笔可以测量产品表面张力以确定是否适宜涂装。
目前有涂料厂家开发了免火焰处理涂料,这种涂料表面张力较低,可以在表面张力较低的基材上成膜,如果基材的表面张力参数符合其要求,可以免去火焰处理工序。
3.热变形温度低
(1)双组分涂料车身用的涂料一般是高温热固性漆,通过高温烘烤使涂料发生交联反应,实现涂层的高性能要求。保险杠要为车身配套,需要达到和车身同样的涂层外观性能和力学性能、化学性能。而塑料件的热变形温度低,不能进行高温烘烤,因而涂料的固化温度受到限制。另外,多数单组分低温烘烤漆的光泽度和耐侯性能较差,很难达到涂层的高质量要求。双组分涂料则很好地解决了这个矛盾。
塑料件保险杠涂装工艺及其设备特点
双组分涂料中的固化剂和涂料混合后发生交联反应,生成长链的大分子,即使在不烘烤的条件下也可以形成高质量的涂层,如果进行低温烘烤又能够避免涂层长时间处于湿膜状态被污染的情况。
关于涂料的选择,以前底漆常采用双组分涂料,但是为了简化工艺及管理,有些涂料厂家研制出了符合质量要求的单组分底漆,现在国内的生产线有些采用单组分底漆,也有些用双组分底漆。由于双组分涂料混合后的粘度会一直上升,时间长了还会变成凝胶状态,色漆一直使用单组分底漆,尤其是金属漆和珠光漆,涂料的粘度对金属粉和珠光粉的排布影响很大,不适宜使用双组分涂料。目前多数塑料件保险杠生产厂家选用双组分聚氨酯清漆,其性能完全可以达到与车身配套的要求,烘烤条件80℃、30min即可。
(2)集中输调漆系统双组分清漆的集中输调漆系统与车身的单组分系统有所不同。对于输调漆输送泵的主泵,国内大多数塑料件喷涂生产线采用成本较低的气动泵,而车身则采用设备成本较高的液压泵。这主要是因为塑料件涂装线的整体投资较低,在输调漆系统上的投资也相应较少。但是运行时,液压泵的液压油一直循环,很少有消耗,其运行成本要比气动泵低很多——约为气动泵的1/3,选用液压泵很快就可以收回成本,并且其噪声小,对调漆间污染小,因此,目前一些新建的塑料件涂装线越来越多地倾向于选择液压输送方式,这种方式在塑料件输调漆系统中已经成为一种应用趋势。
双组分涂料的固化剂和涂料一旦混合,8h内就会固化,涂料厂家一般要求在2~3h内用完。涂料固化后的输漆管道难以清洗,因此要求混合后的管道尽量短。在手工喷涂段,专用的双组分混合装置一般置于喷漆室附近。常用的有GRACO公司的Promix系列混合设备(见图5)。混合后的双组分涂料不可以进行循环,以免固化的涂料产生污染,因此,双组分涂料的循环不像单组分涂料那样可以循环到枪,混合后的涂料只可以循环到涂料混合装置之前。
塑料件保险杠涂装工艺及其设备特点
对于双组分涂料的自动喷涂,机器人的换色阀(见图6)采用双通道设计。换色阀以前未混合的涂料可以回流循环,固化剂采用盲端式,不进行循环。换色阀以后与固化剂混合后的涂料如果未用完则必须排掉。固化剂与涂料的配比采用齿轮泵控制。固化剂的比例可以比要求的比例稍大,以达到完全反应固化的目的,但是绝对不能小,否则固化不完全,会造成涂层无法干透的弊病。喷涂机器人的双组分混合装置一般置于雾化器内,目的也是缩短混合后的管路,减少涂料浪费,减轻清洗的工作负担。
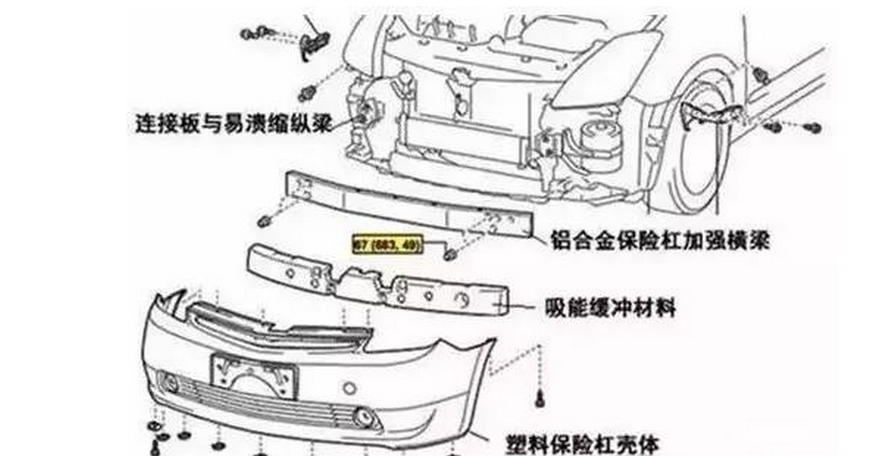
4.强度低
塑料件的强度较低,抗冲击能力差。如果涂层较基材的柔韧性差,一旦受冲击破裂,裂痕容易达到基材表面,无法起到保护基材的作用,因此,保险杠常选用具有一定弹性、柔韧性好的聚氨酯涂料。对涂层硬度要求过高必然会牺牲柔韧性,因此塑料件的涂层硬度不宜过高,要求在HB以下即可。
塑料件保险杠涂装工艺及其设备特点
三、保险杠形状特点引起的涂装工艺、设备的差异
相对车身喷涂而言,保险杠的喷涂面积小,开孔多,采用空气喷涂极易造成过喷,导致涂料大量浪费。同时,过喷的漆雾也使得喷漆室环境恶化,需要经常清洁喷漆室、更换滤袋等。为保证涂装质量和喷涂环境,保险杠喷漆室的风速要求比整车涂装喷漆室要高。
为提高涂料利用率,色漆和清漆常采用静电喷涂的方式。由于静电涂装时喷涂工具(喷枪或旋杯)与产品之间形成了一个高压静电场,通过电场力的作用,涂料粒子沿一定路径运行到产品上放电沉积,显著减少了涂料粒子的分散及回弹。相同的喷涂环境下,空气喷涂的涂料利用率为30%~50%,静电喷涂可以达到70%~80%。采用高压静电喷涂不仅大大提高了涂料利用率,又有利于改善涂装作业环境。选用导电底漆涂装之后,塑料件保险杠的色漆和清漆涂装就可以进行静电喷涂了。
综上所述,本文塑料件保险杠涂装工艺中涉及到的主要参数如表所示。
总结:汽车保险杠和车身同属于户外用品,空间跨度较大,使用时间长,不仅要求具备优良的外观、保光保色性好,还要具备与车身高温漆同等的耐湿热、耐盐雾、耐划伤、耐紫外线和耐化学溶剂性等。塑料件保险杠的自动喷涂生产线通过针对基材的特别处理、涂料的选择以及设备的合理配备,使保险杠的涂层质量不仅达到了以上这些使用要求,同时还实现了大批量、柔性化生产。